EDN Innovation Awards Finalist
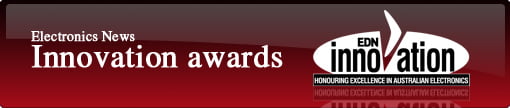
EDN Innovation Awards
This is a bit of a different post. I’m pretty stoked that we are finalists in the 2009 EDN Innovation Awards in 2 separate categories. The award categories are:
- Best Application Of Analogue Design
- Best Application Of Design Software
So I thought I might let you know a bit more about the project, and also give a public thanks to Pablo Varjabedian of Borgtech for allowing us to put the project forward. We design Electronics and Embedded Software products primarily for Australian Electronics Manufacturers. Our focus is outstanding Electronics Design that will propel them into a world class competitive position while delivering improved profit margins. Low Cost Electronics Manufacture but with outstanding performance and reliability.
We routinely use non-disclosure agreements, NDAs, with our clients and so don’t usually get the chance to put our design work forward for awards because we will never disclose a client’s Intellectual Property, IP, without their express permission. In this case Borgtech gave us permission and so we were able. As you can probably see, there is a real benefit to the client in allowing the award application because they also get recognition for the product.
This is also not an unusual project for us. We have done a lot of outstanding work over the 12 years we have been in operation. So it is good to have some of it recognised by the Industry we are so passionate about.
Electronics Design Details
This project was an example of our Project Priorities Perspective in action. In this case Performance was the primary concern with cost coming second and time coming last. We spent the time to get the performance up and the cost down. There was an earlier post on one aspect of this project where we looked at Analogue Electronics as a way to improve battery life in a Low Powered Electronics Data Logger.
The Electronics Design trade offs were:
- OH&S or Operational Health and Safety – must protect users from hazardous voltages
- Low Power Electronics – operates from 3 AA cells for up to 6 months
- Convenience – Analogue front end completely Software Controlled
- High Reading Accuracy – millivolt resolution over +/-10V range with 60dB Mains Rejection
There were many other Design Requirements but the above list are the core Electronics Design Requirements addressed as part of the award nomination. Below I will look at each of these in turn.
Protection From Hazardous Voltages
Now lets look at the hazardous voltage issue in a little bit more detail. The voltages in questions were:
- 5000V, 5KV, for 2 seconds
- 250VAC continuously
These come about due to the conduction of Lightning Strike Transients or Mains Leakage Voltages onto the Pipelines and Storage Tanks monitored for Corrosion Protection status. The Analogue Electronics front end had to provide protection against these cases while meeting all the other Design Requirements. And of course quickly settle so that only the readings during the disturbance were affected.
It also led to the use of an 802.15.4 RF Telemetry Link because this meant the monitoring PC could do Real Time Monitoring without hazard. Many other products in this industry use RS232, RS485 or even I2C connections for monitoring, configuration and upload of the Data Logger Records. In the case of the Borgtech CPL2 you can put it in place and then configure it and start the logging with no danger to the operator apart from the moment of electrical connection. And the initial part of the run can be monitored to ensure everything is correctly set up. Otherwise you could get a months worth of data that was useless.
And finally, because of the power budget and the possibility of the batteries going flat, the Analogue Electronics had to survive the above Abuse Voltages unpowered!
Low Power Electronics
The Borgtech CPL2 is a Battery Operated device. There are several reasons for this but the three most relevant are that it is:
- IP68 sealed against water ingress – it is often installed in a pit that can flood
- Must operate remotely from a convenient power source
- Protects the operator and PC from Transient Voltages since there isn’t a direct electrical connection
But this is also part of the challenge. For convenience it used off the shelf batteries you can buy at any service station. But to get 6 months life required a strong Power Management approach including powering down anything not in use including the Analogue front end. If you are taking a reading every minute over six months then most of the device is off most of the time. In this mode the average Power Consumption is 37uA.
Analogue Electronics – Software Controlled
The Borgtech CPL2 handles both Current Shunt and voltage mode readings. The Analogue Electronics were designed to have a software selectable full scale range of +/-10VDC and +/-150mVDC so that is could do either mode of operation from the same input. The previous model required a different connection for each of these modes and most other models on the market are the same.
And all of this while maintaining accuracy, abuse voltage protection and low power operation.
High Reading Accuracy
By the standards of an Agilent (I still want to call them Hewlett Packard) 6.5 digit laboratory multimeter our millivolt, mV, resolution at +/-10VDC isn’t rocket science. But for a device with the Voltage Abuse Protection and Low Power Electronics requirements we had to meet, it is pretty good. Another small twist you might not recognise is that it is +/-10VDC. This means you can monitor it with the polarity inverted and fix it up later on by inverting all the readings. The previous model was unipolar and so you couldn’t do this meaning you could have just wasted a month. And then there is the live monitoring so you can see what the readings look like before leaving the unit to log away in the background.
EDN Innovation Awards
On 17 September 2009 we know the final outcome but either way I am pretty happy to have the recognition this project has already received.
Ray Keefe has been developing high quality and market leading electronics products in Australia for nearly 30 years. For more information go to his LinkedIn profile.This post is Copyright © Successful Endeavours Pty Ltd.
Hi Ray and Junette
Congratulations on the huge achievement of being a finalist in two categories of the 2009 EDN Innovation Awards. Malcolm and I are looking forward to hearing the outcome!
Congrats for a great success and i hope you will be success in future also.